In this dual interview, Douglas Owen from BIC (Bureau International des Containers et du Transport Intermodal) and Shane Robertson from Stolt Tank Containers (STC) share their insights on the BIC Facility Code, its impact on the tank container industry, and the role of standardisation and IoT technologies in driving a more efficient, transparent, and sustainable supply chain.
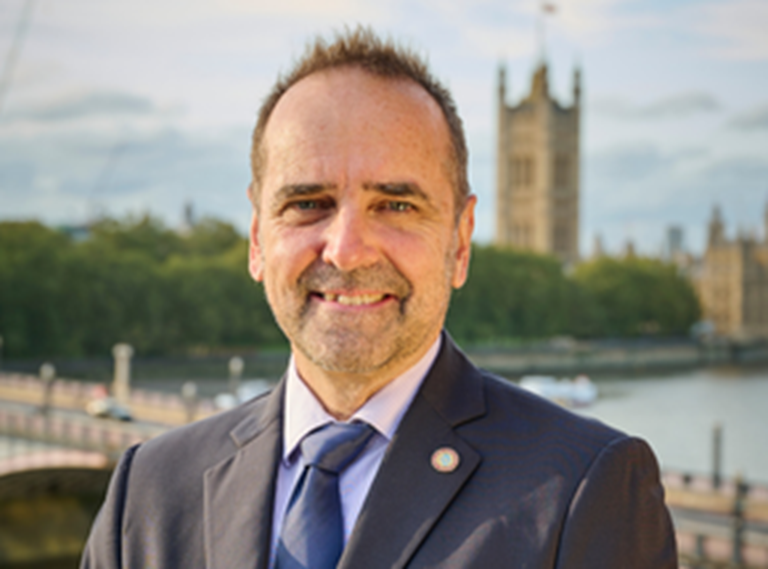
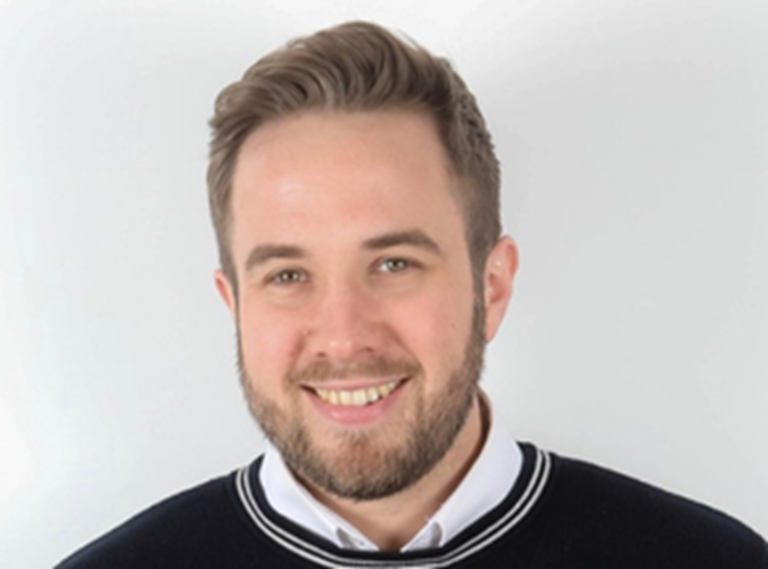
What inspired you to lead the initiative to promote the BIC Facility Code, and why do you think it’s important for the industry as a whole?
Douglas (BIC):
Within the past five years, the industry has recognized that the
fragmented, non-harmonised method of identifying facilities is no longer conducive to the
digitalisation happening across the supply chain. The BIC Facility Code
address these challenges by enabling seamless communication and supporting IoT
integration, helping the entire industry work in harmony. The ultimate goal is
for the industry to adopt a single, harmonised code that will simplify
operations and improve efficiency.
Shane (STC):
At Stolt, we are huge believers in the value of standardisation.
By partnering with BIC, we aim to further digitalise our operations and
streamline processes. The BIC Facility Code enables clearer
communication, reduces confusion, and enhances interoperability across the
supply chain. For the industry, this will lead to a more cohesive and
technologically advanced ecosystem, paving the way for future innovations.
What steps did Stolt take to implement the BIC Facility Code across its depots, and what challenges did your team face in the process? What challenges does BIC see?
Douglas (BIC):
The key challenge for many operators, including Stolt, is ensuring the integration of the BIC Facility Code into legacy systems. For BIC, we’ve focused on promoting industry collaboration, ensuring the harmonisation of facility identifiers with partners like SMDG – and in ensuring that other organizations, such as DCSA, IICL - and now ITCO – adopt the harmonised codes in their own standards. This allows operators to smoothly integrate these standardised codes into their existing systems, reducing friction and operational complexity.
Shane (STC):
At Stolt, we focused on standardising our naming conventions and address formatting across all depots. One of the toughest challenges was defining the exact boundaries for geofences at each facility. This required detailed mapping and collaboration with local teams to ensure accuracy. Thankfully, the BIC’s mapping tool made this reasonably painless. And once we had the geofences in place, we could then integrate these standards into our operational systems for smooth communication across the supply chain.
How will the BIC Facility Code benefit not only Stolt but also suppliers and customers within the tank container industry? Can you provide an example of how this has worked in practice?
Douglas (BIC):
The BIC Facility Code has significant benefits for everyone involved in the supply chain. It helps eliminate ambiguity when communicating between partners, from shippers to customers. For example, the BIC Facility Code used for EDI messages is now integrated with the Global Container Geofence Library, which we’re pleased to see Stolt also making great use of. This allows companies to track the movement of assets in real time, improving transparency and efficiency across the supply chain.
Shane (STC):
For Stolt, the BIC Facility Code simplifies logistics by providing truckers with a clear, standardised code instead of a full address, reducing errors and saving time. One of the best examples is integrating IoT solutions with our geofences. Customers can now track the real-time movement of their containers as they enter or depart our depots, which improves operational efficiency and enhances real-time visibility.
How do you see the future of IoT technologies in supply chain operations? And how does Stolt’s inclusion in the BIC’s Global Container Geofence Library position the company to leverage IoT for real-time tracking and efficiency?
Douglas (BIC):
IoT technologies are a game-changer for supply chains, enabling real-time data and enhanced asset management. With the Global Container Geofence Library, companies like Stolt are well-positioned to capitalize on IoT capabilities. Through this integration, operators can track containers, optimize routes, and respond to issues more efficiently, all while improving the overall service quality.
Shane (STC):
The future of IoT technologies is incredibly exciting. By integrating IoT devices with the Global Container Geofence Library, Stolt has detailed contextual information and can track the location of containers in real time, optimize routes, and respond swiftly to any delays or issues. This positions us to provide better service, enhance efficiency, and improve asset utilization across the entire supply chain. The real-time data will give us the ability to make better decisions faster.
Stolt is one of the first in the tank container business to fully embrace the BIC Facility Code and is helping align third-party depots with the harmonised code. What do you think is holding other tank operators back from adopting these initiatives, and how would you encourage them to join the effort?
Douglas (BIC):
One of the main barriers to adoption is the perceived complexity of the implementation process. Many operators are concerned about the upfront costs and effort required. However, this is more of a perception than a reality. Once operators understand the long-term benefits, such as reduced errors, improved operational efficiency, and better customer service, they are more likely to embrace the change. The key is to have industry leaders like Stolt take the first step and actively promote the benefits of adopting the BIC Facility Code to others.
Shane (STC):
I think the resistance stems from the perceived complexity of implementation and the upfront costs. However, the process is simpler than many might think. At Stolt, we were able to make the transition quickly and see immediate benefits. I would encourage other operators to focus on the long-term rewards - operational efficiency, reduced errors, and improved customer satisfaction. Sharing our success stories and providing collaborative support can help make the transition smoother for others.
What effort and resources should other tank operators invest in to align with the BIC Facility Code, and what can they expect from this process?
Douglas (BIC):
Often there is an initial clean-up of a depot list that needs to take place, but once that is complete it is fairly straightforward; it’s just a question of loading the harmonised codes into systems. When it comes to the geofencing, there is a small time investment required to help draw or review the geofences. But we’re talking about an hour or two per port or city.
Shane (STC):
Operators will need to involve their IT teams and depot teams in the process, especially for the geofencing component. It requires a bit of coordination to ensure you have the right local expert to ensure the geofence is right. But once that is in place, the benefits of leveraging the BIC Facility Code and the Geofence Library are clear: improved communication, efficiency gains, and cost savings.
Key Takeaways: Why Adopting the BIC Facility Code (and Global Container Geofence Library) is Crucial
1. In one sentence, why should other tank operators adopt the BIC Facility Code?
Douglas (BIC):
By adopting the BIC Facility Code, operators can streamline communication, reduce errors, and enhance the efficiency of the entire supply chain.
Shane (STC):
Together, we can help minimize errors that occur when collaborating and improve the efficiency of the industry!
2. What do you both believe the future holds for the tank container industry if this initiative continues to gain traction?
Douglas (BIC):
Fewer emails, fewer mapping tables, fewer delays, safer supply chains, happier customers.
Shane (STC):
A future of streamlined, efficient global operations with enhanced transparency, safety, and reliability, leading to overall industry growth and customer satisfaction.
Looking Ahead: Shaping the Future of Tank Container Operations
This conversation between Douglas and Shane highlights the transformative potential of the BIC Facility Code and its role in standardising operations across the tank container industry. Through their leadership and collaboration, BIC and Stolt are setting the stage for a future where seamless communication, IoT integration, and harmonised facility codes combined with the Global Container Geofence Library will help drive a more efficient, transparent, and sustainable global supply chain.
As the industry continues to evolve, embracing digitalisation, standardisation, and collaboration will be key to unlocking the full potential of the tank container sector, ensuring better operational efficiency, enhanced customer satisfaction, and a more connected global logistics network.
Douglas Owen, Secretary General Bureau International des Containers
Douglas is Secretary General of BIC. An experienced executive with 25 years in the maritime transportation field, Douglas spent over 10 years developing, commercialising and deploying innovative equipment visibility and software tools to help many of the world's biggest ocean carriers and container leasing companies operate more efficiently and control operating costs. Prior to joining BIC, Douglas was Vice President EMEA for International Asset Systems (now part of WiseTech Global).
Shane Robertson, Director Digital & Transformation Stolt Tank Containers
Shane is the Director of Digital and Transformation at Stolt Tank Containers, where he leads a cross-functional team focused on digital innovation, process optimisation, and the integration of advanced technologies into logistics and supply chain operations. With a strong background in business analysis, Shane has implemented strategic initiatives that bridge the gap between technology, customer experience, and operational efficiency. He is passionate about fostering a customer-centric approach while driving transformation and continuous improvement across the organisation.